TIME |
AGENDA |
|
09:00 |
Welcoming Speech, Opening Remarks & Thank You Sponsor Speech By Summit Producer |
|
|
|
09:05 |
How The 1st CLT Hotel In Australia Was Conceived, Re-designed And Completed, With Major Cost Savings And Reduced Carbon Emissions: The 55 Southbank Blvd Hotel Case Study |
|
A top Australian developer, recently rebuilt and completed the first CLT hotel in Australia, now one of the tallest timber buildings in Melbourne. At the original site, the existing commercial office building was able to accommodate a future extension of 6 levels with the use of concrete framed construction. The developer overcame this challenge, using Laminated Timber (CLT) construction which allows for the existing building to support an additional 10 levels, thereby achieving the targeted 220 rooms. In addition to being significantly lighter than concrete, CLT use results in lower transport costs and therefore reduced carbon emissions. Due to the quantum of offsite fabrication, including prefabricated modular hotel bathrooms, the time spent on site is significantly reduced. Sequestered within the timber itself is approximately 4,000 tonnes of CO2 emissions, the equivalent of the annual carbon emissions of 130 homes. The predominant use of this carbon negative material represents an opportunity for the creation of a new paradigm in sustainable construction |
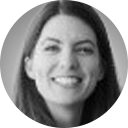 |
Celine Herbiet
Senior Designer
Bates Smart |
 |
|
|
|
09:30 |
New Case Studies Of Steel And Timber Prefab Buildings In Australia: The Lendlease Experience |
 |
George Konstandakos
Head of DesignMake
Lendlease (confirming) |
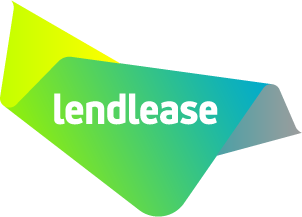 |
|
|
|
09:50 |
How Prefab Is Facilitating The Construction Of High-Quality, Custom Architectural, Sustainable Homes – The US Experience |
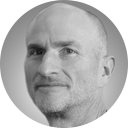 |
Steve Glenn
CEO
Plant Prefab, USA (via video link)
(Plant Prefab is the first prefabricated design and construction company in the United States dedicated to sustainable construction, materials, processes, and operations) |
 |
|
|
|
10:15 |
Morning Refreshments & Networking |
|
10:30 |
Increasing The Scale Of Using DFMA Principles To Unlock Offsite Manufacturing Construction: Lessons Learnt From Newly Completed Prefabricated Projects – Perspective From Mirvac |
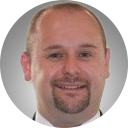 |
David Haller
National Operations Manager, Masterplanned Communities, Construction
Mirvac (invited) |
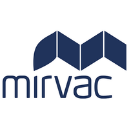 |
|
|
|
11:00 |
Global Exemplar: Delivering State-Of-The-Art PPVC Modular Projects – The Singapore Experience |
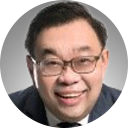 |
Raymond Chan
Special Projects Director
Teambuild Engineering & Construction, Singapore (confirming)
(Global Pioneer of PPVC Technology, Projects & Prefab Bathroom Pods) |
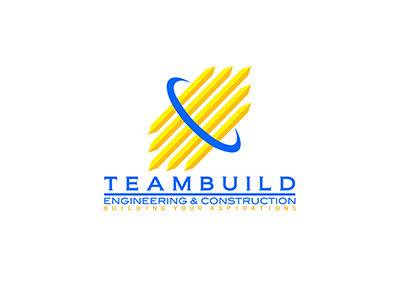 |
|
|
|
11:30 |
New Project Focus: Property Development Potential In The Western Sydney Aerotropolis Precinct, With The Possibilities For Modular Construction In Future Projects |
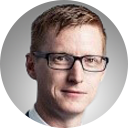 |
Jason Stephenson
Managing Director
Land Evolution |
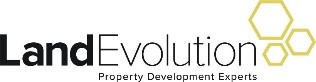 |
|
|
|
12:00 |
Panel Discussion: |
|
- How To Capitalize On New Project Opportunities From New Market Recovery
- Investing In New ConTech: Overcoming Inertia, Optimize New Opportunities
- Managing Funding And Risk Management Challenges In Modular Construction
- Sustainability Innovations And Prefabrication In The Circular Economy
- Advances In Prefabrication And Construction Tech In Australia: Moving Forward With The New Regional Prefab Innovation Hubs. Conceived by the federal government, these regional hubs support the development and growth of prefab in Australia, through increased collaboration between industry and research, support new prefab technologies and improve the prefab manufacturing ecosystem. These are aimed at increasing prefab’s market share from 5% to 15%, creating 20,000 new Australian jobs and adding $30 billion to the economy
|
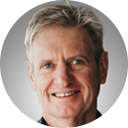 |
Andrew Duffin
Director
NBRS Architecture |
 |
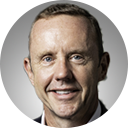 |
Nick Deeks
Managing Director
WT Partnership |
 |
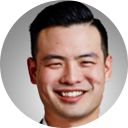 |
Matt Khoo
Managing Director
ICD Property |
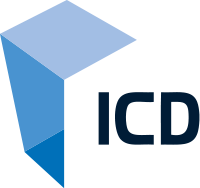 |
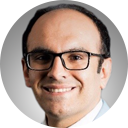 |
Dr Fred Moshiri
Senior Structural Engineer
ACOR Consultants |
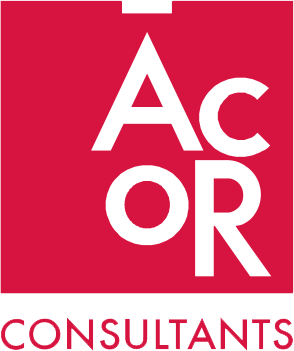 |
 |
Joachim Clauss
Founding Principal
Smartform Architecture |
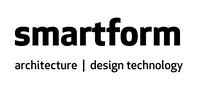 |
|
& Invited Prefab Experts |
|
|
|
|
12:45 |
Lunch & Networking |
|
|
|
|
13:45 |
Healthcare Facility Prefabrication And How Hospital Modular Construction Can Meet The Urgent And Critical Healthcare Needs In An Era Of COVID-19 |
|
Modular construction’s quickened delivery times means industry can provide rapid solutions to the increasing demand of health care facilities. At the outset of the Covid pandemic, some very quick examples of this were witnessed in Wuhan, China. Two modular hospitals were built in just over a week during the Chinese New Year holiday period, in response to strained resources as a result of the outbreak. Modular construction and pre-fabrication are now revolutionizing healthcare with new modular prefabricated designs that will reduce the cost and time taken to build hospitals by 50%. The breakthrough will eventually filter down to benefit a much bigger ecosystem of stakeholders through reduced healthcare costs. |
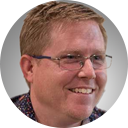 |
Dr Jason Yates
Senior Director, Capital and Asset Services
Queensland Health |
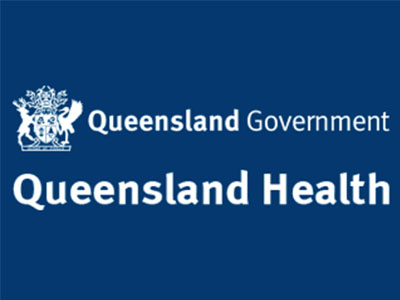 |
|
Modular Construction Of Hospitals And Health Care Facilities In Australia, With Case Study Of Modular Construction In The Health & Aged Care Sectors |
|
- Why the health and the aged care sectors can benefit from modular construction innovation
- Observing COVID Safety and Design Considerations
- Key area focus emphasis on performance based design
- The repeatability, superior quality allows regulators to meet performance requirements
|
|
Senior Management
Hutchinson Builders |
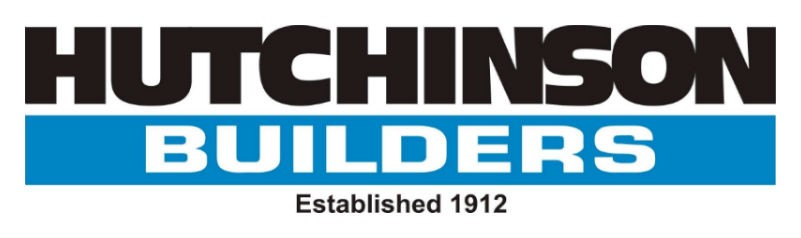 |
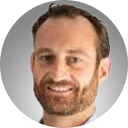 |
Jamie Coe
Prefab Expert and Manager
Hutchinson Builders |
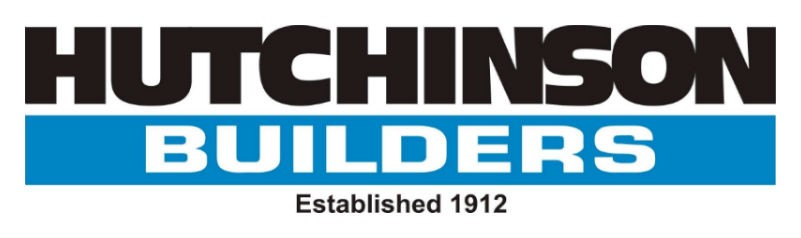 |
|
|
|
14:30 |
Prefabrication In Sydney: Planning For And Designing The World’s Tallest New Hybrid Timber Tower In Sydney’s “Silicon Valley” |
|
Sydney will soon be home to what is claimed to be the world’s tallest hybrid timber building. Owned by Australian tech giant, Atlassian, it will be constructed using timber, steel and glass, right in the heart of Sydney’s new Tech Central Square. The $1 billion-plus building will have approximately 35 floors and will feature natural ventilation and large planted terraces. The hybrid construction could use 50 percent less embodied carbon than conventional techniques and, once completed, use 50 percent less energy for maintenance than a conventional building. It will also feature solar panels and operate on 100 percent renewable energy from the day it opens. Using Mass Timber Construction (MTC) techniques, this project entails a steel exoskeleton that supports the rest of the structure. The building will stand in the Tech Precinct at Sydney’s Central Station which will help to drive the area’s recovery from coronavirus and form part of a planned regeneration that will provide workspace for 4,000 in the Atlassian building alone. Offices around the world have closed due to the coronavirus pandemic and some companies have told employees they will be working from home for good. This planned building will respond to the new realities of working life. The project is designed to operate on 100% renewable energy and reach net zero emissions by 2050. The tower’s steel exoskeleton incorporates an electricity-generating façade system with self-shade capabilities to reduce direct heat gain. Combined with the use of mass timber, the façade enables the project to leverage Sydney’s temperate climate to help reduce carbon emissions and generate on-site energy. |
|
|
|
|
|
|
14:45 |
A Developer’s Perspective: Bridging The Gap Between Construction And Manufacturing |
|
Prefab Construction. Case studies of creating new bespoke living spaces utilizing CLT. CLT is 30% Lighter than Concrete and Steel, Improves Construction Costs by 15% and Promises 50% Lower Carbon Footprint |
|
- Case Study Of The $47 Million Hotel Constructed On Top Of An Existing Office Building Using CLT
- Case Study Of The $3 Million Oakleigh Child Care Centre Showcasing How CLT Can Be Used To Achieve Design Outcomes
• Our choice of material (CLT) & design consultants
• Building regulations (as they relate to CLT)
• Builder appointments and outcomes from the owner’s point of view
|
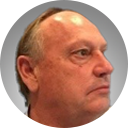 |
Tim Davey
General Manager, Projects
Hume Property (invited) |
 |
|
|
|
15:15 |
Afternoon Refreshment & Networking |
|
|
|
|
15:30 |
How And Why To Develop Zero Energy Modular Buildings |
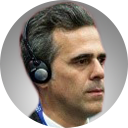 |
Furio Barzon
Founder & CEO
Green Prefab, Italy (via video link) |
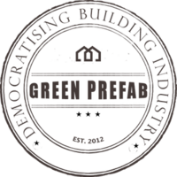 |
|
|
|
16:00 |
Fast-Tracking Design Delivery, With Case Studies On Data Centers And Other Infrastructure Transportation Or Utility Projects: Prefabrication As The Strategic Option |
|
Data centers are the core foundation infrastructure that fuel the Tech Boom and is needed for new economic growth. Ultimately, data is what runs the world and with major impact events like Covid19, there is a natural acceleration in demand for data center services as people try to share or simply stay informed. Prefabrication can provide a quick and convenient solution to data center construction. Prefabrication reduce risk by eliminating site works and delivery delays. With a complicated data center project that has short delivery timelines, pre-engineered product packages, along with prefabricated solutions, could be the answer. As demand for data storage grows rapidly, so too is the demand for scalable and easily installed data centers.
Prefabricated elements—precast concrete and steel are now used for the cut-and-cover Sydney Metro stations—including the first-time use in Australia of precast wall elements for soil-retaining applications. Up to 80% of the main structural elements of a Sydney Northwest Metro Station are prefabricated, including 50-tonne box beams spanning up to 22 m. The main elements of the “leaf” canopies were also prefabricated and erected on site. Placing the canopies with cranes required accurate positioning to allow connection to the four supporting points situated on buttresses. Once connected to their buttresses, temporary propping was secured to allow installation of the bracing elements. The use of prefabrication for long-span trusses resulted in more than a 40% reduction in steel weight. The innovative prefabrication design at this station increased the efficiency and sustainability of the station project, both in construction and in future maintenance operations.
|
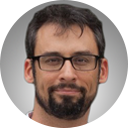 |
Charles Fortin
Managing Director
Collard Maxwell Architects |
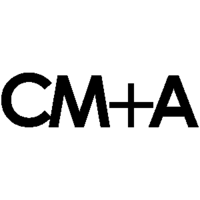 |
|
|
|
16:30 |
Interactive Roundtable Discussions |
|
- Advances In Timber Materials And Technology For Prefabrication
|
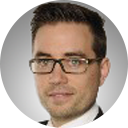 |
Arthur Walch
CLT/Timber Manager, Asia Pacific
Binderholz GmbH, Germany |
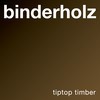 |
|
- Modular Construction For BTR (Build-To-Rent) Projects: How Modular Construction And Offsite Pre-Fabrication Can Deliver Faster Build Rates, Higher Quality Finish For BTR, With Case Studies
- Modular Homes Made For Bushfire Areas
- New Steel And Concrete Prefab Projects & Opportunities
- Home Office Pods For WFH
- Green Steel For Modular Construction
- Advances In AS3850 Precast
- Precast Concrete Stairs Innovation
- Prefab Column Systems Innovation
- Introducing Better Quality Building Components & Products
- Exploring Airspace And Rooftop Modular Homes
- Securing The Finance And Insurance For Builders/Developers & Managing The Cash Flow
- Prefabricating The NSW’s Education Infrastructure
- Prefabricated Prefinished Volumetric Construction, PPVC
- Advanced Prefab Bathroom And Kitchen Pods
- Plumbing Prefabrication Opportunities
- Mass Timber Regulations In International Building Code
- Blockchain For Construction Practice
- Integrating Renewable Technologies (Solar & Microgrids) With Modular Green Building Design
- Advances In New Construction Materials: Bamboo, Hemp
- New Prefabrication Construction Techniques And Technologies
- 3D Printing A Smart City: New Breakthroughs
- Drones For High Rise Fire Fighting, Risk Based Integrity Inspection And Site Surveying
- Sustainable Prefab: Recycling Plastic Waste For Manufacturing Prefab Building Components
|
|
|
|
17:30 |
Closing Remarks By Summit Chairman |
|
|
|
|
|
|
|
|